So I've been too lazy to mount the new tank yet,but I did get motivated to start on the hydraulic clutch conversion. And I need some advice.
First off,it took fooorever to get the clutch cover trued up in the lathe. Pretty close to an hour actually. But I got the centered bored out for the slave cylinder mount and I also leveled the three mounting lugs for the outer cover. This will allow for the new cover I have in mind.
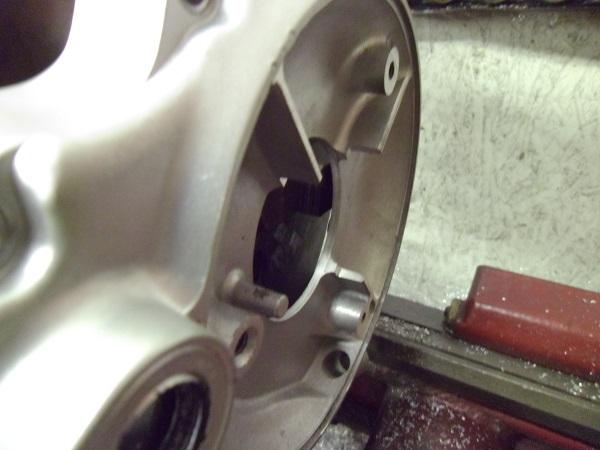
Very humble beginnings. I made this mount out of a scrap piece and Im pretty sure it's too short. I think the pushrod that will connect the slave cylinder to the pressure plate will need more support (lengthwise)than what this will allow(more on that later),but it gives you an idea of what I'm going after.
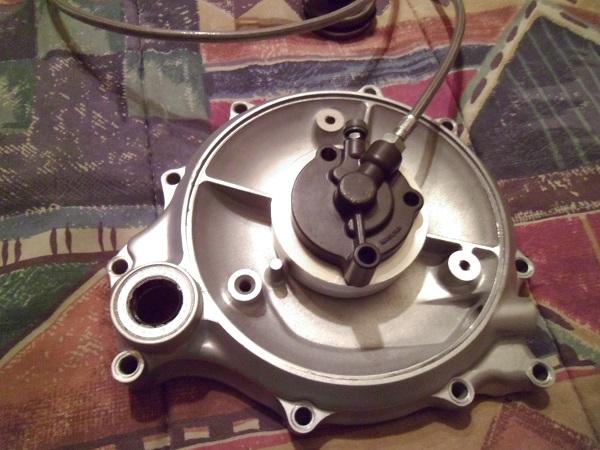
If you look at the piston in the slave cylinder you see a divot in the center. A single ball bearing goes there,so I have the option to let the pushrod spin with the engine vs. the stock setup where the clutch pushrod is static.
I'll weld the mount to the cover and the slave cylinder has an o-ring where it mounts up,so it'll be easy to seal it all up.
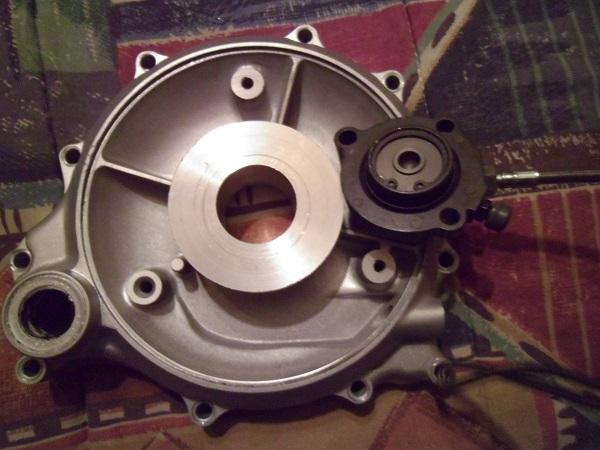
The pressure plate has a pretty beefy ball bearing where the stock pushrod comes in to contact with it,but remember the stock setup is not in constant contact-it runs with slack in the setup so this bearing does not turn nonstop. Only when you pull in the clutch lever.
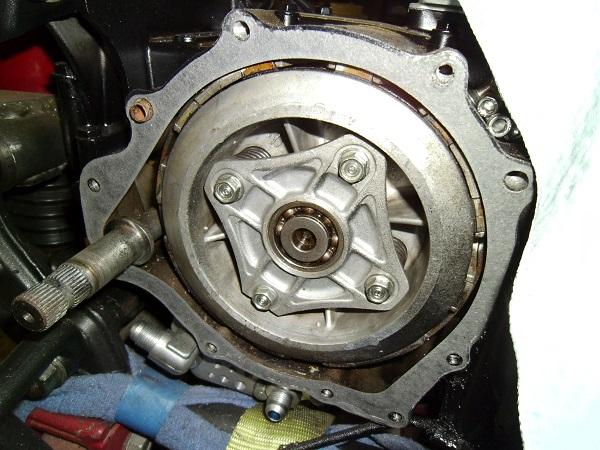
And that where I need advice: should I run a static pushrod or allow it to spin?
Now,since this slave cylinder is self-adjusting there will be no slack in the system. The pushrod will remain in contact with the slave cylinder piston and the throwout bearing on the pressure plate at all times. This is not an issue with the slave cylinder since it is designed for this. Personally,even though it's not running in constant contact in stock form, I think the stock throwout bearing will hold up to constant duty since it's such a pretty beefy little dude and it does have a constant supply of oil. But,if the pushrod is allowed to spin between these two bearings it will obviously need it's own bearing to spin in as well. That's where I need advice. My idea on this is to use a needle bearing without an inner race and let the pushrod ride directly on the needles.Remember,it has to slide freely to and fro inside the bearing to actuate the clutch. If I make the pushrod out of polished stainless steel and it rides on the needles will that hold up,or do I need tool steel for this?
The other idea is to build a captured pushrod that doesn't spin and eliminate the bearing issue for the pushrod. That still has the throwout bearing serving constant duty,but that's gonna happen either way. In my mind this would be best since no moving parts means no possible wear,but how would I make a pushrod that is captured/doesn't spin? It would still need a bushing to slide on,but that's simple to work out. The only way I can think to make a captured pushrod is to make one with an ear on it that rides in a keyway in the bushing. The ear and keyway are two things I dont have the tools to pull off. And I don't want to farm out any machine work. I'd rather do it all in house if possible.
So,any ideas? Hit me up,please.